基礎知識
ソルダーペーストとは?
目次
成分や使用方法についてご紹介
近年、自動車や家庭用電化製品などで多機能化が進んでいます。それに伴い、基板に使用される電子部品の小型化・搭載数増加が進み、基板と部品を接合する製造工程である「はんだ付け」が重要な要素となっています。小型化の進んだ電子部品を確実にはんだ付けするためには、「ソルダーペースト」を用いた表面実装技術が重要です。本記事では、今後もはんだ付けの主流となるソルダーペーストの成分や、使用方法などについて解説します。
- ソルダーペーストとは?
- 成分
- ソルダーペーストのはんだ粉末Type(グレード)
- 保管方法と使用期限
- 使用方法
- 使用されるアプリケーション
- まとめ
ソルダーペーストとは?
ソルダーペーストとは、粉末状のはんだ合金と、フラックスと呼ばれるロジンを主成分としたペースト状の樹脂を混合したもので、「クリームはんだ」や「はんだペースト」と呼ばれる場合もあります。SMT(表面実装)用として、プリント基板上に印刷して電子部品を実装する際に使用されます。部品の小型化に対しては、より微細で高い印刷精度が要求されるため、ソルダーペーストの印刷性能は実装品質に大きな影響を及ぼします。印刷不良、実装不良を避けるため、ファインピッチ実装に適切なソルダーペーストを選択する必要があります。ここからは、ソルダーペーストについて下記の2点をまとめます。
- 成分
- ソルダーペーストのはんだ粉末Type(グレード)
はんだ粉末Typeは、想定する仕様に合わせたソルダーペースト選びの参考にしてください。
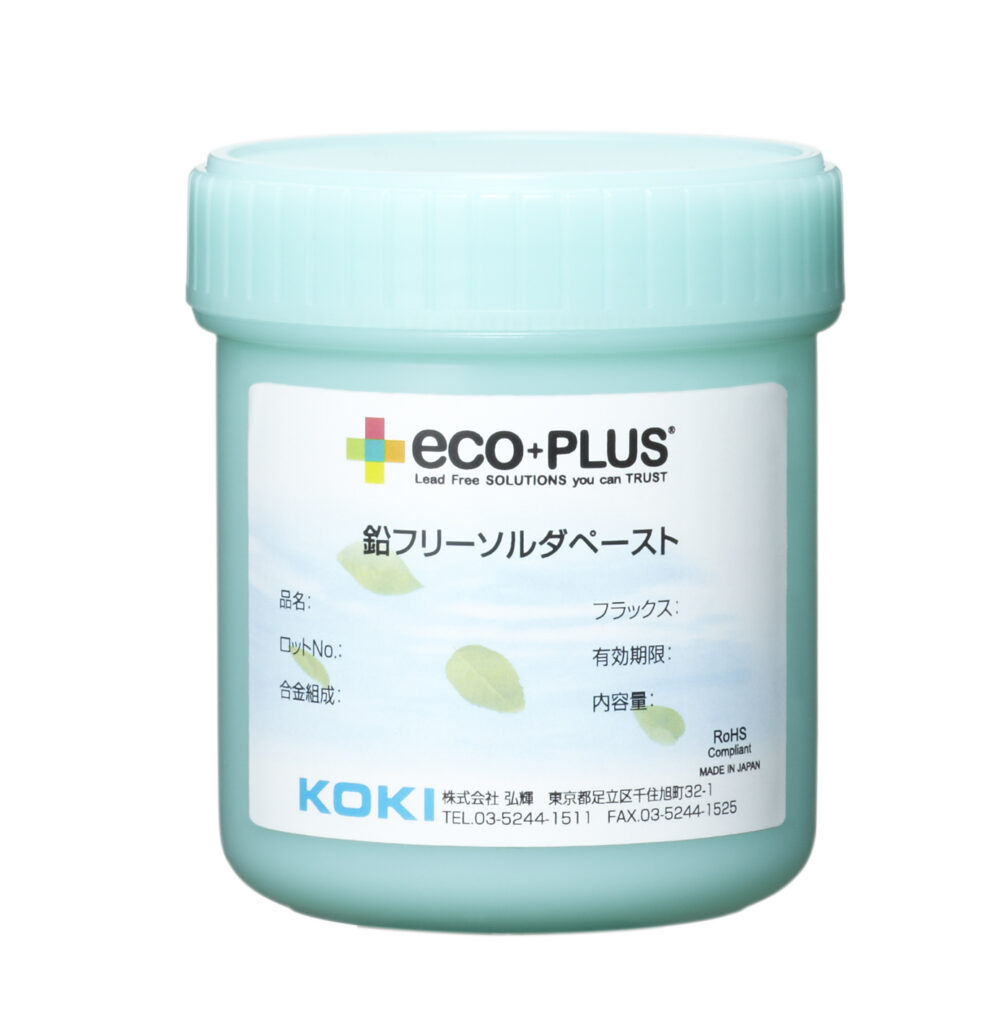
成分
ソルダーペーストの成分は、大きく「はんだの粉末」と「フラックス」の2つに分けられます。一般的な鉛フリーはんだの粉末は、錫、銀、銅の金属を混合したもので、粉末の形状には、球形と不定形があり、現在ではほとんど球形が使用されています。粉末の粒径はさまざまであり、主流のサイズは20〜45μmクラスです。残りの成分であるフラックスは、主にロジン・合成樹脂などの樹脂、添加剤としての活性剤やチキソ剤、粘度調整用の溶剤で構成されています。フラックスの役割は次の通りです。
- 部品接合部の金属表面に酸化皮膜があると、はんだとの接合が妨げられるため、酸化被膜を除去します。
- 酸化被膜を除去しても、はんだ付け時の温度ですぐに酸化被膜が再生されてしまいますので、フラックスが被膜する事で金属表面の再酸化を防ぎます。
- はんだは表面張力が高いので、濡れ広げさせるためにはんだの表面張力を下げる作用もあり、はんだ付けに必要不可欠な役割です。
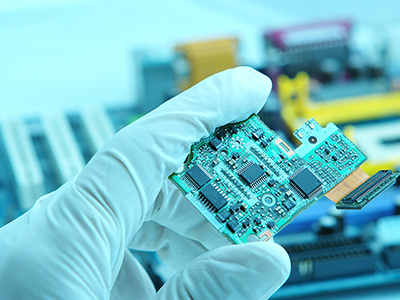
ソルダーペーストのはんだ粉末Type(グレード)
ソルダーペーストのはんだ粉末TypeをIPC規格J-STD 005に基づいて分類したのが表1です。
Type | 粒径(ミクロン) |
---|---|
1 | 75-150 |
2 | 45-75 |
3 | 25-45 |
4 | 20-38 |
5 | 15-25 |
6 | 5-15 |
7 | 2-11 |
8 | 2-8 |
部品のサイズや、ソルダーペーストを印刷する条件によりはんだ粉末Type選びが重要となります。主に民生用電子機器ではType3か4、スマートフォン等の小型電子機器では、Type4か5が使われます。粒径が小さくなると、コストが高くなる傾向があるとともに、不濡れ、未溶融といった不具合の発生頻度も高くなるため、フラックスによる対策が必要となります。
保管方法と使用期限
次は、ソルダーペーストの保管方法と使用期限についての解説です。基本的に、ソルダーペーストは冷蔵保管する必要があります。温度が高くなると金属が酸化したり、はんだの粉末とフラックスが反応してしまったりするためです。ただし、なかには常温で保管可能なソルダーペーストもあります。ソルダーペーストの使用期限は、保管方法や製品にもより異なりますが、未開封冷蔵保存で6ヵ月から12ヵ月程度です。使用期限を過ぎると、ソルダーペーストの粘度が上がり固くなり、印刷不具合が発生しやすくなります。使用期限内での使い切りをお勧めします。
使用方法
ソルダーペーストは、印刷・マウント・リフローの3つの工程を経て使用します。最初の工程は、ソルダーペーストのプリント基板の上への印刷です。1枚のプリント基板に搭載される電子部品の数は多数で、サイズも年々小さくなっているため手作業による印刷は困難なため、自動装置によって、高速で正確に印刷が行われます。
次にマウント工程は、ソルダーペーストを印刷したプリント基板の上に、チップ抵抗やコンデンサをはじめとした様々な種類、サイズの電子部品を乗せていきます。
最期にプリント基板へのマウント完了後、リフロー炉に入れて加熱し、ソルダーペーストを溶融させます。プリント基板上の電子部品を同じ加熱条件ではんだ付けできるため、接合品質のバラツキを抑えられます。
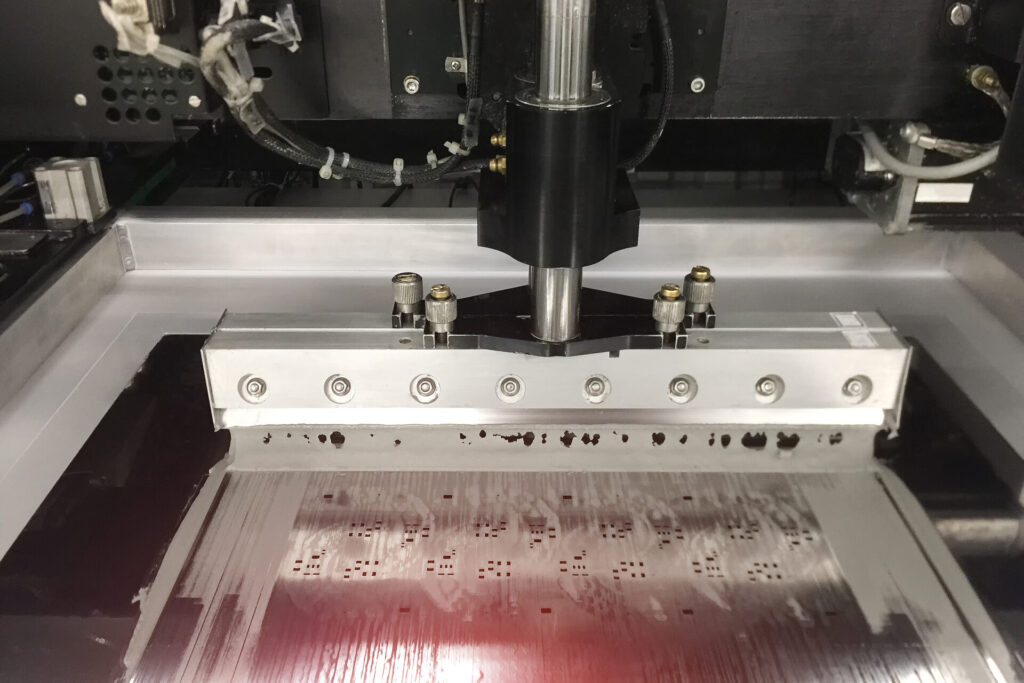
使用されるアプリケーション
印刷工程で使用されるアプリケーションは、ソルダーペーストを供給する方法に合わせて3タイプあります。1つ目は、手作業で行う場合です。研究・実験段階では、大量に基板を作成せずに、条件を変えながらソルダーペーストを塗布します。この場合は、シリンジや手印刷にて一つひとつ塗布していきます。
2つ目は、印刷機、メタルマスクを使用した印刷です。ソルダーペーストを塗布したい場所に穴の空いたメタルマスクを、プリント基板に重ねソルダーペーストを一気に印刷塗布します。プリント基板からメタルマスクを剥がすと、穴の開いている部分にソルダーペーストが塗布されます。手作業よりも速く正確に作業できます。
3つ目は、ディスペンサー(塗布装置)です。インクジェットプリンターのような動きでプログラムされたとおりにヘッドが動作し、ソルダーペーストを塗布していきます。シリンジに充填したソルダーペーストを正確な場所に適量を塗布する性能が求められます。
次に、マウント工程で使用されるアプリケーションがマウンターです。ソルダーペーストが塗布された場所に、部品をピックアップして正確に乗せていきます。
リフロー工程では、リフロー炉が用いられます。リフロー炉は複数のゾーンから構成された温風加熱炉で、ゾーンごとに加熱・冷却の設定が可能です。基板、部品の種類や、ソルダーペーストの種類により、温度や炉内の酸素濃度などの細かい管理が求められます。
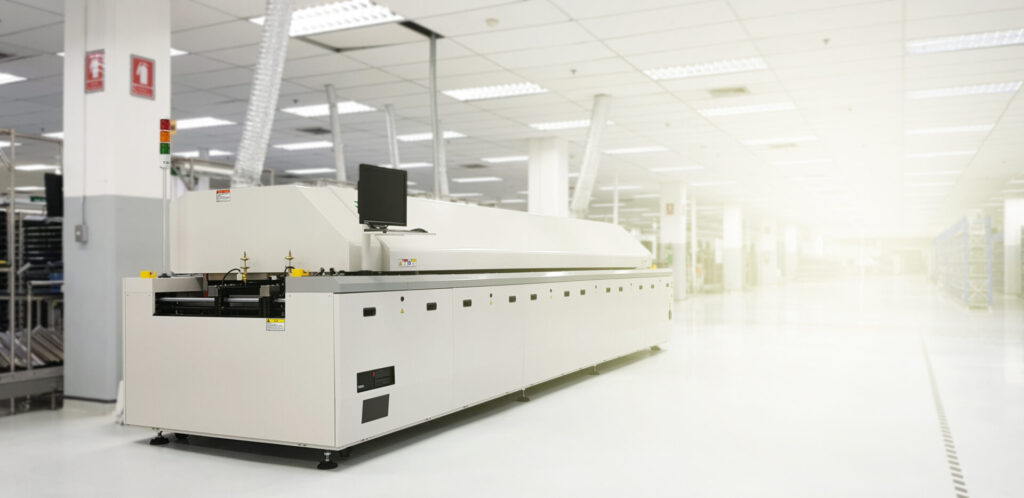
まとめ
ここまで、電子部品の基板実装製造に欠かせないソルダーペーストについて、成分や使用法についてご紹介しました。今後ますます高機能化、高密度化する基板実装において、ソルダーペーストに求められる性能もより多様化していきます。目的に合ったソルダーペースト選びのために本記事を参考にしてください。